The Titan Structure - In conversation with Head of Production - James Bate
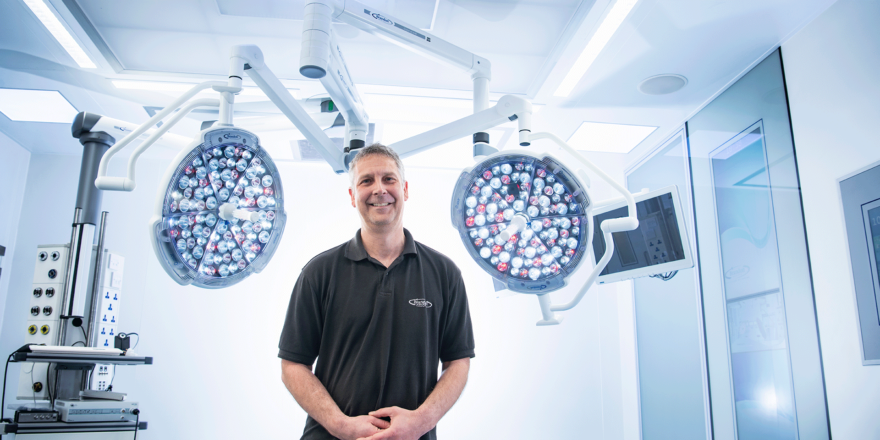
In your own words, what is the Titan Structure – how would you describe it to someone who knows nothing about it?
The Titan Structure is the central axis system; in other words, it is the main fixing from which we can hang/attach all our operating lights or other products, such as monitors.
What was your role/how were you involved within the Titan Structure project – what were your responsibilities?
Although I oversee the work in production, I was quite heavily involved in the design process before the Titan Structure came into assembly. This was because I was able to bring a slightly different insight to the design engineers (who mainly work using Computer Assisted Design – CAD rather than with the physical product.) therefore, I was able to spot ideas that could be improved, ultimately, I was involved in rolling out the structure into production.
During the Titan Structure project, have you worked in a team or individually – do you prefer group projects or working by yourself, and do you think there should be more teamwork within projects?
As I oversee the work in production and assembly, I can work with multiple people every day therefore, I’m constantly working in a team. Working within a team is much more beneficial than working individually, as multiple people are involved, offering many differing opinions, expertise and insights. Teamwork creates the best products in the shortest time period, as your colleague may spot a mistake or problem that you cannot.
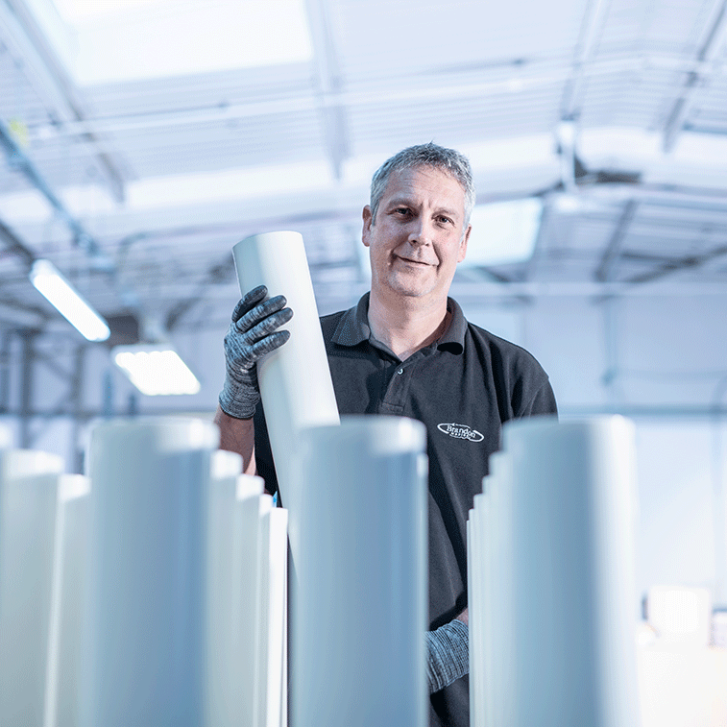
“Safety is a fundamental aspect of Brandon’s products, mainly due to the fact that they are installed in hospitals, veterinary practises, and other institutions within the medical sector therefore, risk aversion and safety of patients, doctors and all individuals who interact with our products is essential.
The safety aspect of Brandon’s products is reflected in the environment we work in; we have a health and safety team, many precautions, and the vast majority of our work is standard practice therefore, yes, I feel safe and supported.”
There are lots of safety features on the Titan Structure; is safety a large/important aspect of Brandon’s products, and does this extend to the environment in which you work – do you feel safe and supported?
Safety is a fundamental aspect of Brandon’s products, mainly due to the fact that they are installed in hospitals, veterinary practises and other institutions within the medical sector therefore, risk aversion and safety of patients, doctors and all individuals who interact with our products is essential. The safety aspect of Brandon’s products is definitely reflected in the environment we work in; we have a health and safety team, many precautions, and the vast majority of our work is common practice therefore, yes I feel safe and supported.
As there are multiple teams to tackle different problems within the project, are there conversations and communications between each team, and do you think this communication worked well in the Titan Structure project?
The Titan Structure was a really positive project that helped Brandon take a step in the right direction towards a more communicative relationship between production, RND and design. With the progression of the project, communications and conversations also developed and, looking forward, Brandon aims to incorporate this additional discussion in future projects as it was extremely efficient in creating a practical product, fast.
What were the aims of this project, and do you think you, and your team, achieved these aims?
Our production team didn’t necessarily have specific aims they had to complete. However, we were part of the process to develop the Titan Structure, and that product in itself had aims. In terms of the structure, the Titan definitely achieved its aims in being lighter and more agile, as the Mk IV was very heavy and cumbersome. Also, by reducing the weight of the product, the Titan completed its aims in cost reduction from the Mk IV.
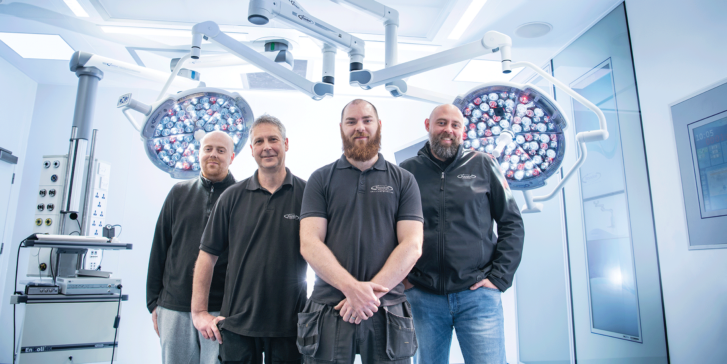
More information about the creation of the Titan Project.
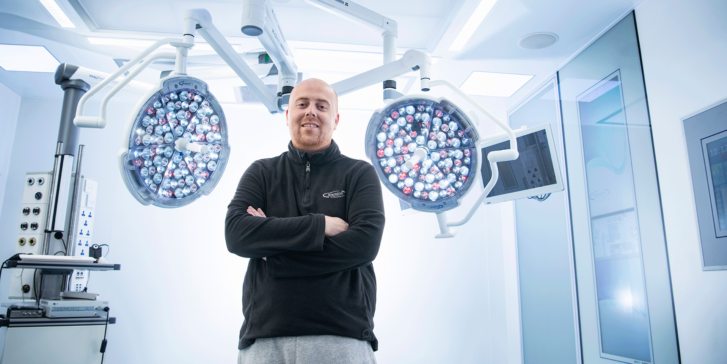
Read about Jack’s experience on the Titan project as the Sigma Assembly Specialist.
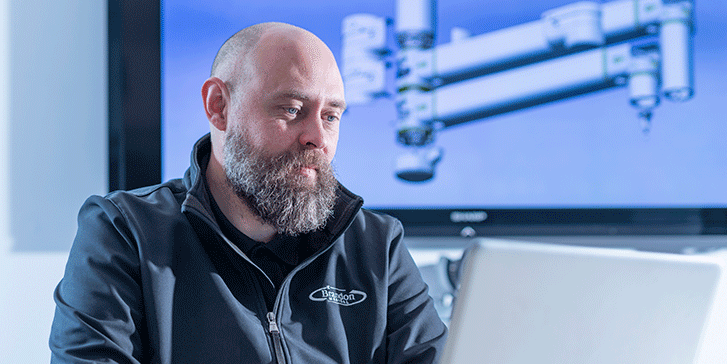
Lead Designer, Peter North, describes his experiences and the benefits of the new Titan Project.
Recent articles

Operating tables have evolved from static platforms into intelligent systems that enhance surgical precision, patient safety, and workflow efficiency. This article explores emerging innovations—from robotic integration to AI positioning—and how they’re reshaping the surgical environment.

The Wall of Knowledge: Transforming Operating Rooms with Brandon Medical’s Integrated Technology
Brandon Medical’s Wall of Knowledge combines Medicontrol™, Symposia®, Entoli™, and PACS/CoPAX to deliver a fully connected, intelligent operating room that enhances surgical decision-making and patient care.

Reinsberg Group Aquires Protec X-ray
BHM group Expands Reinsberg Group with Acquisition of German X-ray Systems Manufacturer PROTEC