The Titan Structure - In conversation with Lead Designer - Peter North.

In your own words, what is the Titan Structure – how would you describe it to someone who knows nothing about it?
Fundamentally, it’s the platform on which all of our operating theatre equipment is mounted, for example lights, monitors and any number of end devices you can conceive of. It is the articulating arm system that it all mounts on and it’s the foundation of everything we do.
What was your personal role/how where you involved within the Titan Structure project – what were your responsibilities?
I was the lead designer, so I designed the Titan Structure, tested it and put it into production with the help of other colleagues.
During the Titan Structure project, have you worked in a team or individually – do you prefer group projects or working by yourself and do you think there should be more teamwork within projects?
This project was started before Toby, the other mechanical design engineer who worked for Brandon Medical. Therefore, I did a lot of the work myself – in terms of the mechanical design elements – but Toby later got involved with some of the design. However, you cannot complete an entire project in isolation as it’s a collaboration between all different departments to get something finished and produced. I could not fully complete the project by myself as there is no point in designing something that cannot be built or specified, and our customers have to understand what the product is.
What were the Titan Structure’s objectives, and how wide was the scope; was there anything that limited the project’s success?
There were many objectives within the project; one of the most important ones, for us as a business, was cost reduction for the customer. The previous central axis structure (the industry term for the Titan Structure) was around 15 years old. Therefore, we learnt so much over that time about what our customers needed and how we could design and build it more efficiently. Another core objective, alongside cost reduction, was to increase the ability to configure the product, to increase its agility and response time.
Why do you enjoy this problem-solving aspect of design? Is this process satisfying and exciting or stressful and daunting?
Design is problem-solving. For me, it is the most fun part as, ultimately, the more problems you solve, the better the product you create and design is. This is because, for us, the issues belong to our clients. Therefore, if we can find solutions to them, we can help our customers.
Brandon Medical’s company values stem from trust, innovation, partnership and doing the right thing; what progress do you think you, as a company, are making in using these values on a day-to-day basis – including this project?
The company values were adopted in this project throughout. The genesis and the core of any project starts by talking to our colleagues and our customers. It is specifically essential to talk to different people within the organisation as, for example, the sales have a different set of requirements to the production team. Therefore, you must be able to engage with your colleagues in a friendly and honest way. Otherwise, communication becomes limited, ultimately limiting our ability to produce and deliver successful products. I believe Brandon is so successful because it is a highly communicative and collaborative company; there are no ‘walls’ here. Many individuals have been with us for a long period of time, so we have a sense of familiarity and community as we are all working to pull in the same direction.

The company values were adopted in this project throughout. The genesis and the core of any project starts by talking to our colleagues and our customers.
It is specifically essential to talk to different people within the organisation as, for example, the sales have a different set of requirements to the production team. Therefore, you must be able to engage with your colleagues in a friendly and honest way.
The Titan Structure has lots of modern features, such as the updated aesthetic of the arms; personally, do you think the function is more important than the physical look of the product or are they equally as important?
Both the function and the aesthetic of a product go hand-in-hand as both are incredibly important. If we produced a product that was technically excellent but wasn’t attractive, customers would not gravitate towards it. Universally, consumers expect well-designed products – in every aspect of their lives – not even specifically within our business. Both consumer products and industrial products require captivating aesthetics as this is the immediate impression a customer gets; most are not able to see the intricacy and innovation inside the product therefore the outside surface must be reflective of the complexity of the mechanical design within.
The Titan Structure also contains many features that provide greater flexibility to cope with complicated installations (for example, the existing stem that attaches the Titan Structure to the ceiling can be reused, and if it cannot be easily removed, vertical spacers can be used to adjust the lamp head height). How important is it to think about the different customer scenarios, and does this, therefore, mean you have to create several additional features for the Titan structure?
There are lots of features therefore, there are lots of ways of configuring and installing the Titaproduct. The creation of these accommodating features stems from years of experience of talking to customers, installers and maintainers as we therefore understood what problems the Titan Structure needed to solve. This was another core objective of the product as we wanted to take the decades of experience we have as a company, and as individuals within the company, and distil that down into a product we could build and sell.
The Titan Structure also has some features built on the design of existing products to provide improved features, benefits or performance. What is the most challenging, to improve an existing design or to start with a blank piece of paper?
It is always easier to improve a pre-existing product as you are able to discover problems and features that need to be improved along the way more easily. With an existing product, there is already a foundation of work to stem from, feedback from customers or colleagues and clean-sheet design is simply much more work. Designing a product from scratch involves hundreds of hours and multiple people to produce something of value. At Brandon Medical, we are constantly improving and developing; nothing ever remains static as we tackle problems and issues immediately whether they be in manufacturing, cost reduction and configuration.
The Titan Structure project was a large-scale project – do these projects ever feel overwhelming and, if so, how could we improve how we run new product development projects at Brandon Medical?
It’s easy to be overwhelmed by a large project, particularly when there are lots of other individuals involved and you’re trying to coordinate all those people in a common direction. However, to cope with this potential stress, every product is designed and sold in smaller, more manageable sections. Therefore, provided everyone points in a common direction, it doesn’t feel overwhelming but rewarding to see something you’ve designed become a real-life product.
What was your favourite part of the Titan Structure project and why? What was your least favourite/ most challenging part of the Titan Structure project and why?
One of the most enjoyable aspects of the Titan Structure project, and any other project, is the social element of talking to people who are interested in what you are doing and collaborating with them. For example, although we don’t closely work together, I often speak to the sales team and the service/installation team. This effort to include them is positive because, sometimes, they feel they do not have a strong enough voice within the process as they aren’t always on site. Another rewarding aspect is presenting the final product, as you can see your ideas and concepts in a physical prototype. However, the slightly less stimulating aspect of large-scale projects like these is the volume of work that is not particularly interesting or challenging but is very much necessary and required for the project’s success.
What motivated you whilst you were working on this project/working for Brandon in general?
Designing and manufacturing products, at its core, is about improving people’s lives – no matter, if it is commercial or industrial therefore, ensuring our customers’ lives are made easier, is an aspect at Brandon Medical that we aim to reflect on as much as we can. We try not to lose sight of this goal as it is easy to do when you are deep in a challenging project.
What were the aims of this project, and do you think you, and your team, achieved these aims?
We have achieved the aims established on our specification (which is a similar concept to a Wishlist with some added weight and strength on the ‘wishes’) as we have reviewed the product against what we set out to do. The Titan Structure project has met the vast majority of its aims. However, there were slight features we had to drop as they were not required or practical for the structure, but we are still continuing to develop the Titan Structure; it is not a static product. Overall, it is a very successful project as it has hit its targets. We continue to produce it without significant problems, proving it to be a highly reliable product.
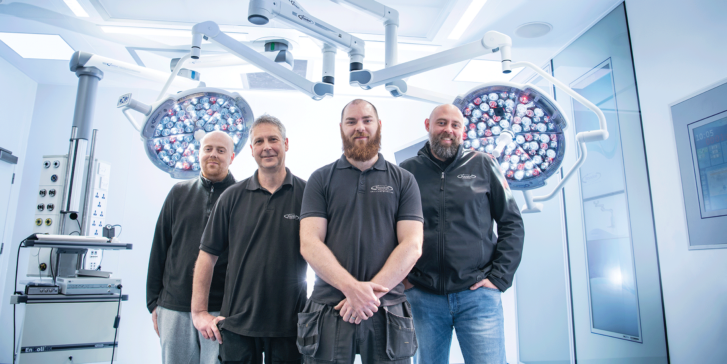
More information about the creation of the Titan Project.
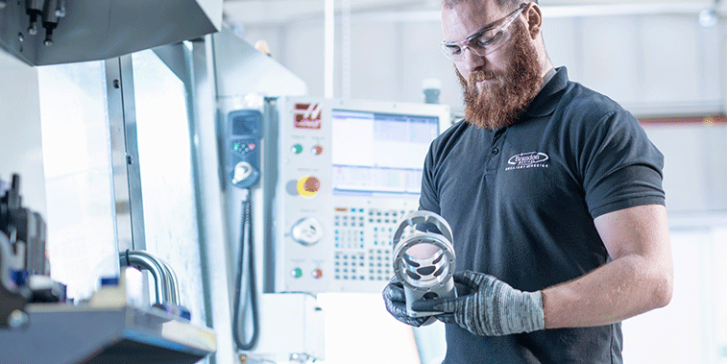
Interview with Head of Manufacturing for the Titan project – Paul Cawthrone.
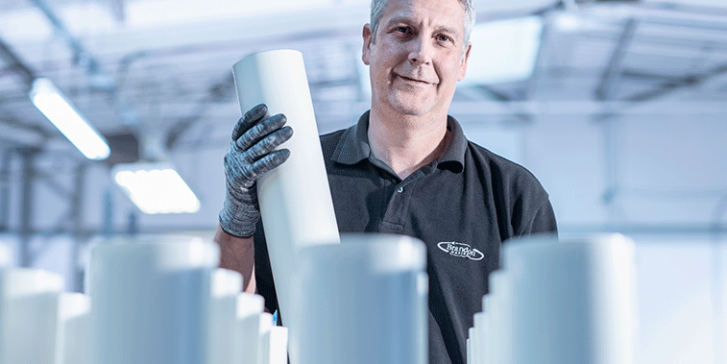
In conversation with Head of Production, James Bates, on his experiences with the Titan Project.
Recent articles

Evolution of operating tables: advancing surgical precision
Operating tables have evolved from static platforms into intelligent systems that enhance surgical precision, patient safety, and workflow efficiency. This article explores emerging innovations - from robotic integration to AI positioning - and how they’re reshaping the surgical environment.

The Wall of Knowledge: Transforming Operating Rooms with Brandon Medical’s Integrated Technology
Brandon Medical’s Wall of Knowledge combines Medicontrol™, Symposia®, Entoli™, and PACS/CoPAX to deliver a fully connected, intelligent operating room that enhances surgical decision-making and patient care.

Reinsberg Group Aquires Protec X-ray
BHM group Expands Reinsberg Group with Acquisition of German X-ray Systems Manufacturer PROTEC